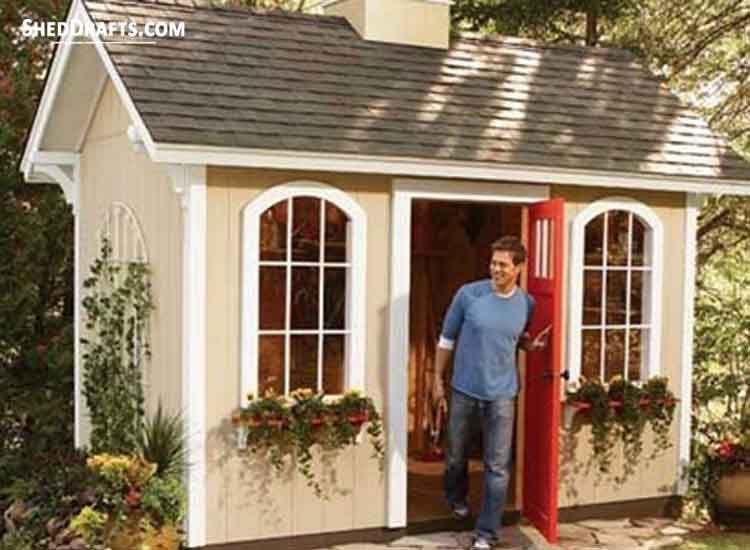
Step-by-Step 8x12 Shed with Loft Plans for All Skill Levels
This comprehensive guide provides detailed instructions for constructing an 8x12 shed with a loft, catering to builders of all skill levels. From beginner-friendly explanations to advanced techniques, this plan ensures a successful project, regardless of your experience. We will cover all aspects of the construction process, from initial planning and material acquisition to the final finishing touches.
Phase 1: Planning and Preparation
Thorough planning is crucial for a successful shed construction. This phase involves several key steps:
1.1 Site Selection and Preparation
Choose a level, well-drained location for your shed. Consider proximity to power sources and accessibility for material delivery. Clear the area of any vegetation, rocks, or debris. Mark the shed's footprint using stakes and string to ensure accurate placement. Obtain any necessary permits from your local authorities before commencing construction.
1.2 Design and Material Selection
This 8x12 shed with a loft design utilizes pressure-treated lumber for the foundation and framing to ensure longevity and resistance to rot and insect infestation. Consider using composite decking or treated lumber for the exterior cladding. For the roof, asphalt shingles provide a cost-effective and durable solution. The loft floor will require robust construction to support the anticipated weight. A detailed materials list is provided in Appendix A.
Consider the following design elements:
- Foundation Type: Concrete slab, pier and beam, or a combination thereof, depending on your budget and soil conditions.
- Roof Pitch: A minimum of 4:12 pitch is recommended for effective water runoff.
- Window and Door Placement: Strategically place windows and doors for optimal ventilation and light.
- Loft Access: Plan for a safe and convenient access point to the loft, such as a fixed or pull-down ladder.
1.3 Tool Acquisition and Safety Precautions
Gather all necessary tools before starting the project. This includes measuring tapes, levels, saws (circular saw, hand saw), drills, screwdrivers, hammers, and safety equipment such as safety glasses, work gloves, and hearing protection. Always prioritize safety by wearing appropriate personal protective equipment (PPE) throughout the construction process. Familiarize yourself with the operating instructions for all power tools before use.
Phase 2: Foundation Construction
A stable foundation is critical for the longevity and structural integrity of your shed. This section details the construction of a concrete slab foundation, a common and effective choice.
2.1 Excavation and Formwork
Excavate the area according to the dimensions of your shed, ensuring a level base. Construct formwork using pressure-treated lumber to create a perimeter for the concrete pour. The formwork should be plumb and level to guarantee a flat and even slab.
2.2 Concrete Pour and Curing
Pour the concrete into the formwork, ensuring proper consolidation to eliminate air pockets. Level the surface using a screed board. Allow the concrete to cure for the recommended time (typically 24-72 hours) before proceeding with further construction. Proper curing is essential to achieve the desired strength and durability of the foundation.
Phase 3: Framing and Wall Construction
The framing forms the structural skeleton of your shed. Precise measurements and accurate assembly are vital for a square and stable structure.
3.1 Floor Framing
Construct the floor frame using pressure-treated lumber. Install floor joists according to the specified spacing in the plan. Securely fasten the joists to the foundation using appropriate fasteners. Ensure proper leveling and alignment throughout the process.
3.2 Wall Framing
Assemble the wall frames using pressure-treated lumber and appropriate connectors. Ensure the frames are square and plumb before fastening. Install window and door openings according to the design plans. Proper bracing is crucial to maintain the structural integrity of the walls.
3.3 Roof Framing
Construct the roof trusses or rafters according to the chosen design. Ensure proper spacing and secure fastening to the top plates of the walls. The roof structure should be adequately braced to withstand wind loads. For the loft, construct a separate floor frame supported by the existing wall framing.
Phase 4: Exterior Cladding and Roofing
This phase focuses on the exterior finishes, ensuring weather resistance and aesthetic appeal.
4.1 Sheathing and Exterior Cladding
Install exterior sheathing (e.g., plywood) over the wall framing. This provides a solid base for the exterior cladding. Apply your chosen cladding material (e.g., composite decking, treated lumber, vinyl siding). Ensure proper overlapping and sealing to prevent water penetration.
4.2 Roofing
Install underlayment over the roof framing to protect the structure from moisture. Install the chosen roofing material (e.g., asphalt shingles) according to the manufacturer's instructions. Proper flashing around chimneys, vents, and other penetrations is crucial to prevent leaks.
Phase 5: Interior Finishing and Loft Construction
This phase involves completing the interior finishes and constructing the loft.
5.1 Loft Construction
Construct the loft floor using appropriate lumber and fasteners. Ensure adequate support to handle the anticipated weight. Install the chosen loft access method (e.g., fixed ladder, pull-down stairs).
5.2 Interior Wall and Ceiling Finishing
Install interior wall sheathing and finish with your chosen material (e.g., drywall, plywood). Install insulation to enhance energy efficiency. Finish the ceilings using appropriate materials and techniques.
5.3 Doors and Windows
Install the doors and windows, ensuring proper weather sealing to prevent drafts and water infiltration. Use appropriate hardware and fasteners.
Phase 6: Final Touches and Inspection
The final phase involves finishing touches and a final inspection to ensure compliance with building codes and safety standards.
6.1 Painting and Finishing
Paint or stain the exterior and interior surfaces as desired. Seal any exposed wood to protect it from the elements. Apply any necessary trim and mouldings.
6.2 Final Inspection
Conduct a thorough inspection of the entire structure to ensure proper construction, safety, and compliance with all applicable building codes. Address any necessary repairs or adjustments before declaring the project complete.
Appendix A: Detailed Materials List (This section would include a comprehensive list of all materials needed, quantities, and sizes. This is omitted for brevity in this example.)
This detailed guide provides a comprehensive framework for building your 8x12 shed with loft. Remember to consult local building codes and obtain necessary permits before commencing construction. Safety should always be your top priority. With careful planning and execution, you can successfully construct a durable and functional shed that meets your specific needs.
No comments:
Post a Comment
Note: Only a member of this blog may post a comment.